Shanghai ESU has launched the E3 series of the third-generation special 3D printers for molds
Introduction: In recent years, metal 3D printing technology has been widely applied in the field of mold manufacturing. The mold industry is experiencing an unprecedented technological transformation. With the gradual deepening of its application, metal 3D printers specialized for molds have emerged as the times require.
On April 15th, 2025, Shanghai ESU Laser Technology Co., Ltd. (hereinafter referred to as "ESU") officially released its third-generation series of special 3D printers for molds — the E3-420 and E3-520. The launch of this new product marks an important step that the mold manufacturing industry has taken towards additive manufacturing.
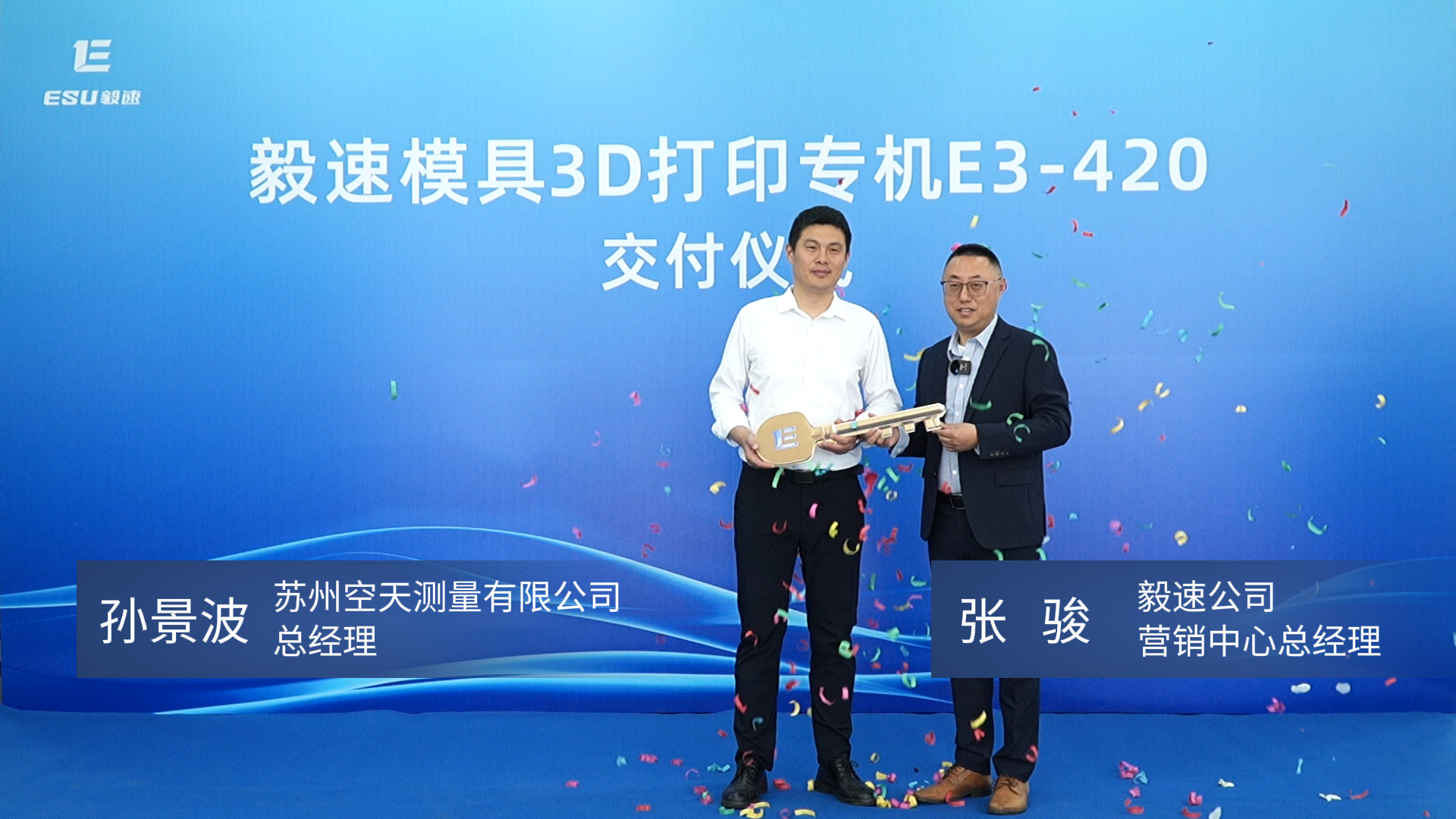
The delivery ceremony of ESU E3 - 420
Specialized Tools for Mold 3D Printing: E3-420 and E3-520
The E3 series is the third-generation of special 3D printers for molds launched by ESU, which is specifically developed for the mold industry. The equipment adopts a multi-laser system (either a 2-laser or a 4-laser option is available). The maximum forming sizes are 400×400×420mm and 400×400×520mm respectively, which can meet the needs of most mold manufacturing. The special process package for mold 3D printing and the rapid grafting function equipped with it can help mold enterprises quickly get started and apply it efficiently. In addition, the imported optical components and the redundant safety design of multiple sensors can ensure the stability and reliability of the equipment during long-term operation. Moreover, the efficient powder handling module and the rapid gas purging function can further improve the production efficiency.
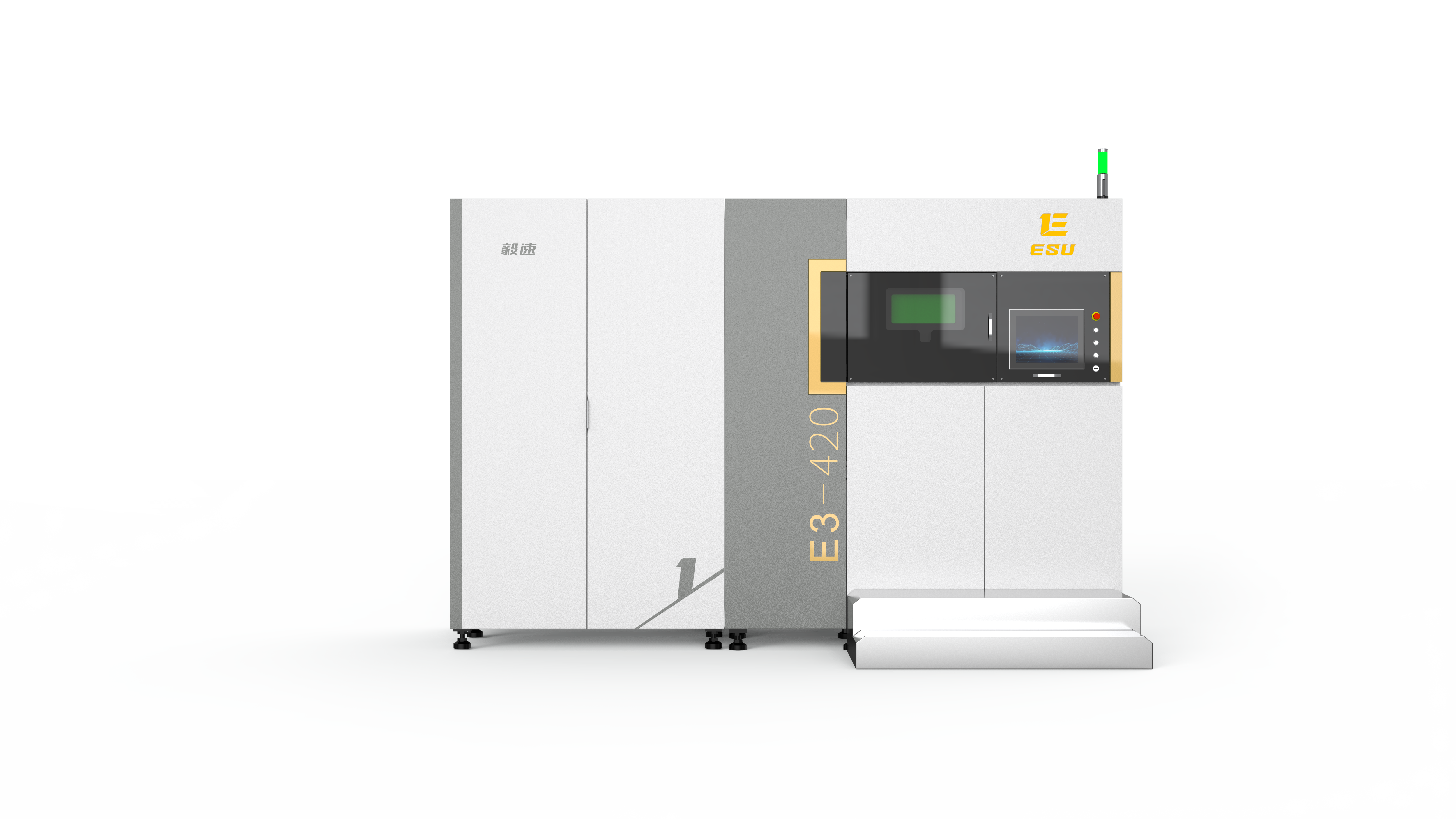
The third-generation special 3D printer for molds of ESU —— E3-420
The person in charge of ESU stated: Currently, there are quite a number of mold manufacturers who, despite having 3D printing equipment in their factories, still come to ESU for printing services. Why are these pieces of equipment "lying idle"? The reason, upon investigation, is that compared with ordinary parts, mold printing not only requires materials to have high wear resistance, high corrosion resistance, high thermal conductivity, and high precision, but also demands that there be no sand holes, no cracks, and that it can meet the requirements of mirror polishing. Therefore, it requires the coordination of equipment, materials, technology, and applications to solve this difficult problem.
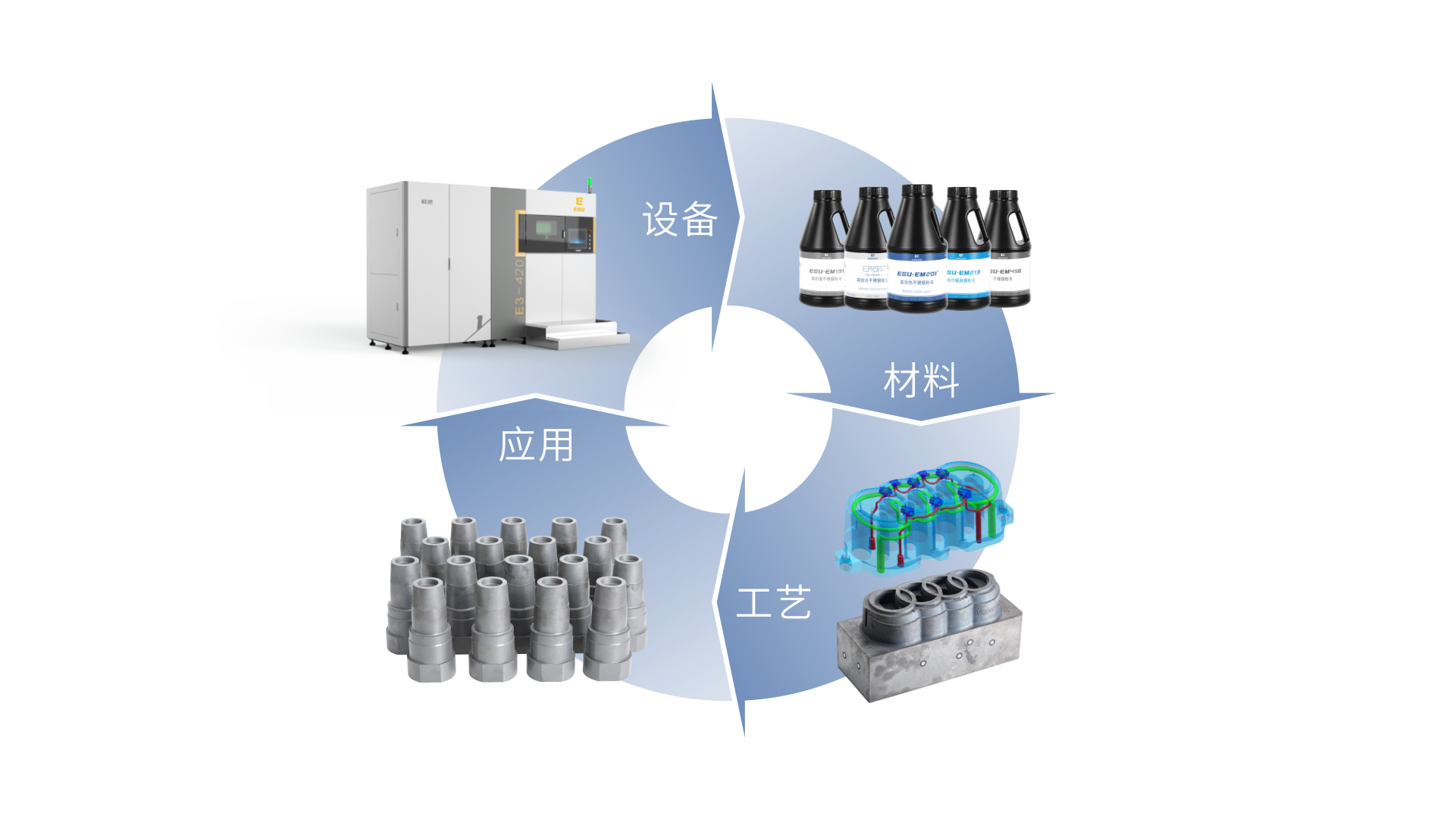
Specialized Materials for Mold 3D Printing
In order to better meet the needs of users in the mold field, ESU has developed several types of 3D printing materials specifically designed for the mold industry, including:
ESU-EM400 High-Polish Mold Steel: Suitable for molds that require mirror polishing, and the polishing grade can reach A1.
ESU-EM300 High-Wear-Resistant Mold Steel: Its wear resistance is approximately 1.5 times that of traditional materials, and it is suitable for high-wear environments.
ESU-EM201 High-Thermal-Conductivity Mold Steel: With a thermal conductivity as high as 80W/m·K, it is suitable for molds that require rapid cooling.
ESU-EM213 Hot Work Mold Steel: Its impact toughness is approximately twice that of H13, and it is suitable for high-temperature working environments such as die-casting molds.
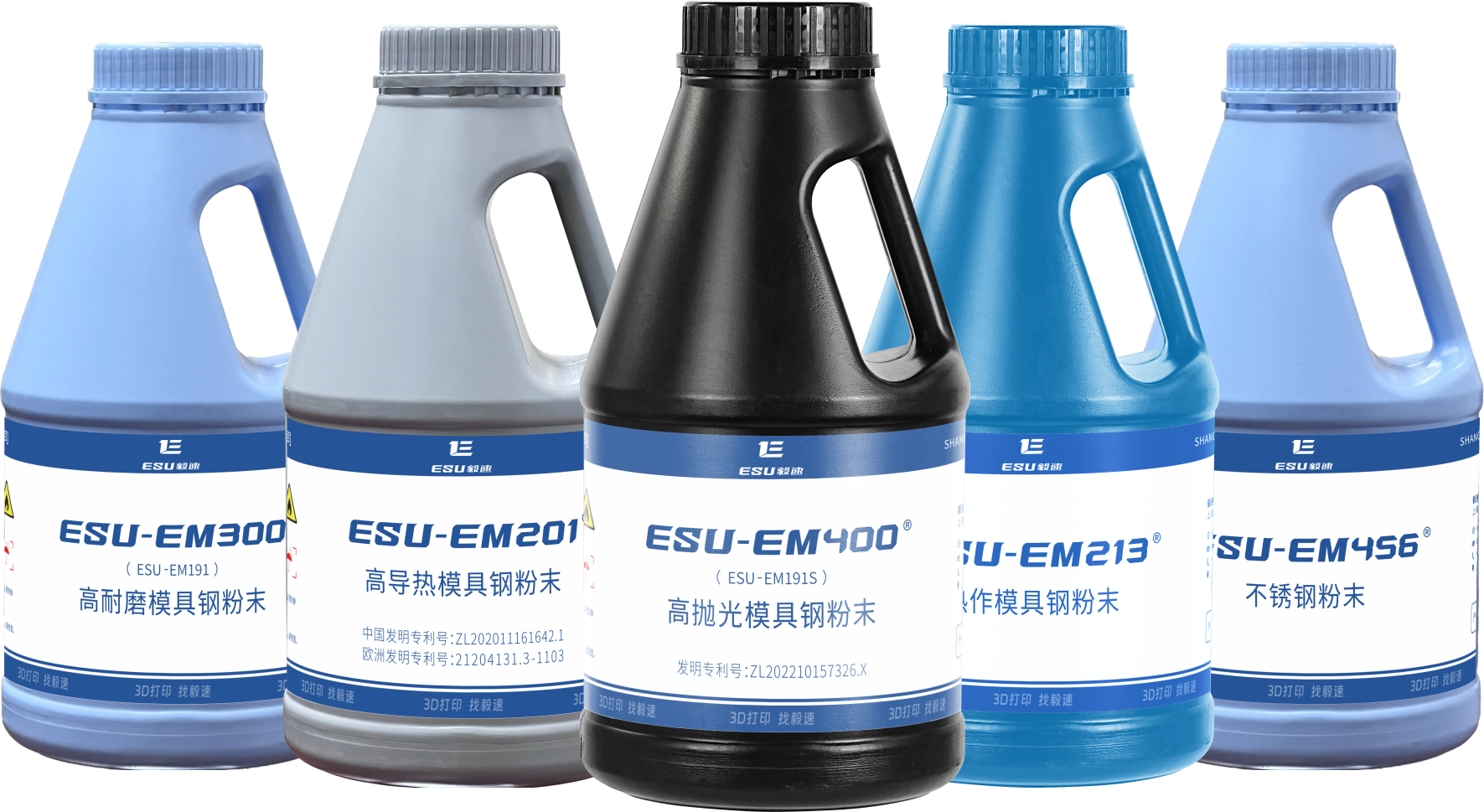
These materials can meet diverse requirements such as being easy to print, having high wear resistance, high corrosion resistance, high thermal conductivity, and high polishability, and they solve the pain point in the mold industry that 3D printing cannot be widely applied due to the lack of suitable materials.
Specialized Processes for Mold 3D Printing
In addition to excellent equipment and materials, the research on processes is also crucial for the quality of printed products. ESU has been deeply engaged in the segmented field of mold 3D printing for many years, and thus has accumulated a complete set of mature printing processes, such as:
Conformal Cooling Channels: The cooling channels printed by 3D technology are evenly distributed along with the cavity, which can achieve more uniform and rapid cooling, significantly improve the product quality, greatly shorten the molding cycle, and increase the production efficiency.
Permeable Steel Process: When 3D printing mold parts, the permeable areas can be arbitrarily specified, which effectively solves the problem of air entrapment during the molding process, reduces surface defects of products, and improves the product quality. In addition to the mold field, permeable steel also has a large number of applications in gas filtration and water filtration scenarios.
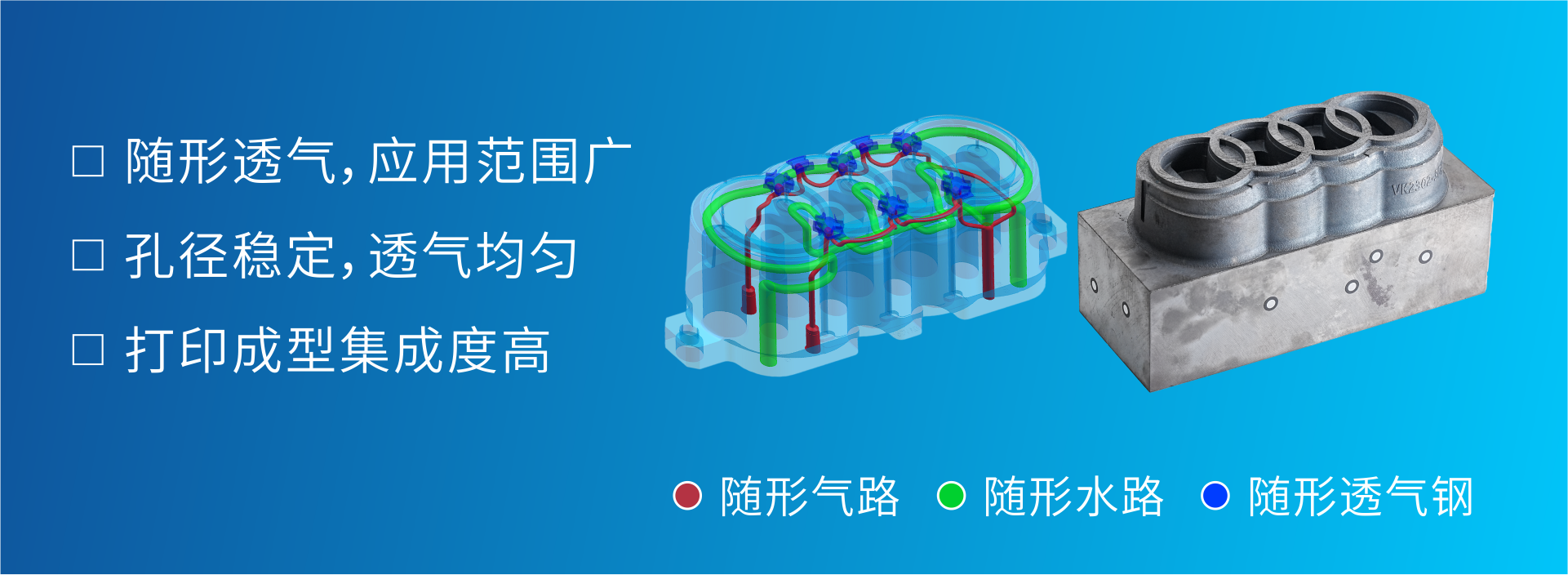
Grafting Process: For large components such as mold cores, the assembly positions are manufactured by subtractive manufacturing, and the forming positions are manufactured by additive manufacturing. Two different materials are grafted together, ingeniously integrating the respective advantages of additive manufacturing and subtractive manufacturing, taking both cost and usage effect into account.
No-Finishing Printing Process: Through precise printing and forming, the dimensions and surface roughness of workpieces can meet the application requirements in some scenarios without the need for precision machining, thus improving production efficiency and reducing production costs.
Zero-Point Positioning: A unified datum interface is adopted to ensure a seamless connection of the mold from the 3D printing platform to the post-processing equipment. It enables rapid loading and unloading of the base plate, as well as quick clamping and datum acquisition with machining equipment. This improves efficiency and ensures accuracy.
These specialized processes in the mold industry can ensure that the printed molds are superior to those manufactured by traditional methods in terms of both performance and service life.
Over 200,000 application experiences in mold 3D printing
Since its entry into the mold industry in 2007, ESU has been deeply applying metal 3D printing in the mold field since 2018. It has served more than 2,000 customers and accumulated over 200,000 application cases, winning wide recognition and praise from the industry. Head - of - the - class enterprises such as HP, Foxconn, Flex, Jabil, and BYD have chosen ESU as their partner. ESU is a company that has a better understanding of 3D printing in the mold industry and a better understanding of molds in the 3D printing industry.
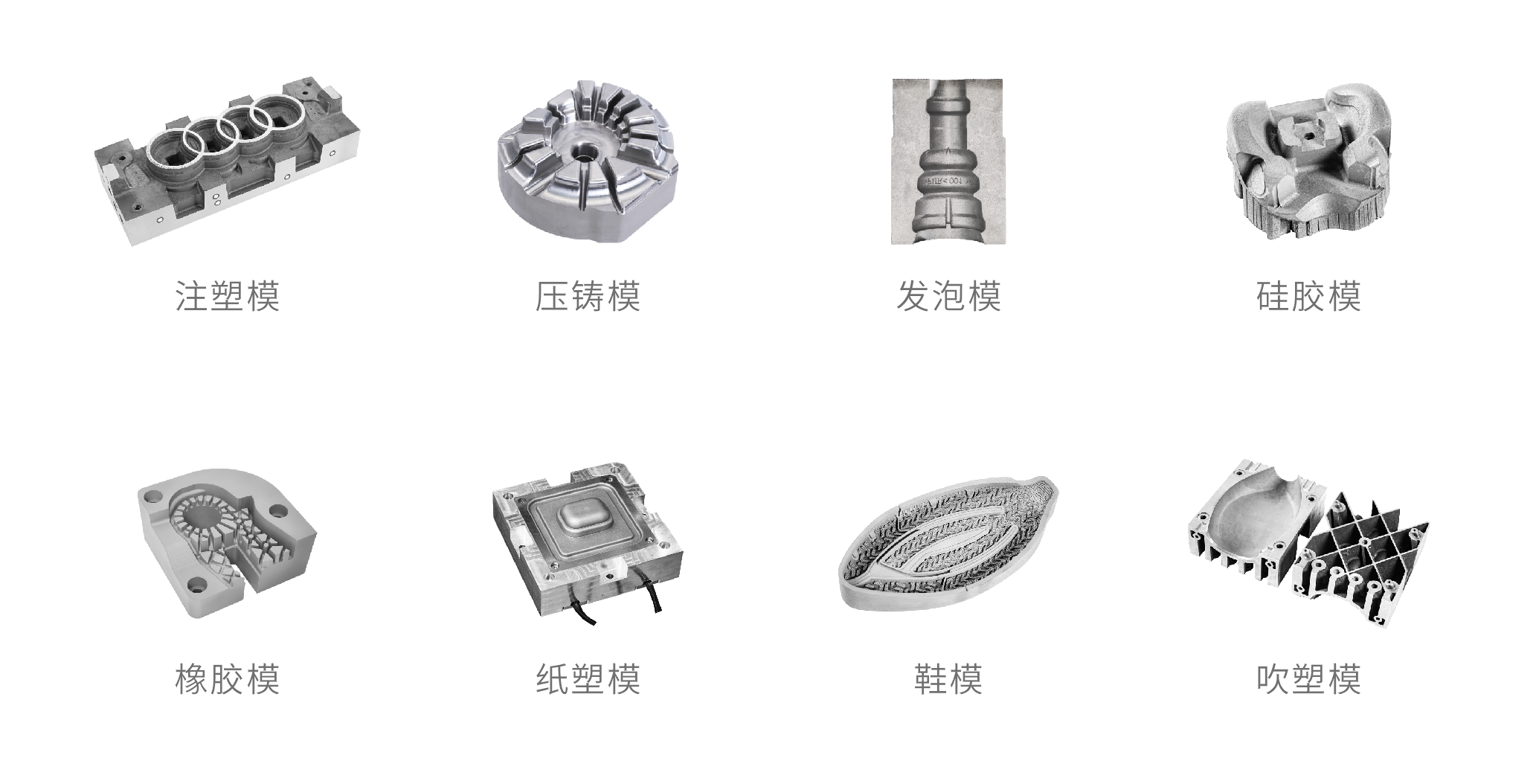
The "Overall Solution for Mold 3D Printing" Emerges as the Times Require
Based on the above-mentioned technological closed loop of special equipment for molds, special materials for molds, special processes for molds, and application experiences in molds, ESU is now empowering Chinese mold enterprises with this complete set of "Overall Solution for Mold 3D Printing".
After comprehensively and truthfully investigating and understanding the users' needs, pain points, and investment expectations, the professional team of ESU conducts a feasibility analysis of the overall solution for the users. This includes configuring special equipment for mold 3D printing, special materials, special processes, and supporting auxiliary machines, as well as carrying out site planning and personnel training. Finally, long-term operation and maintenance services are provided.
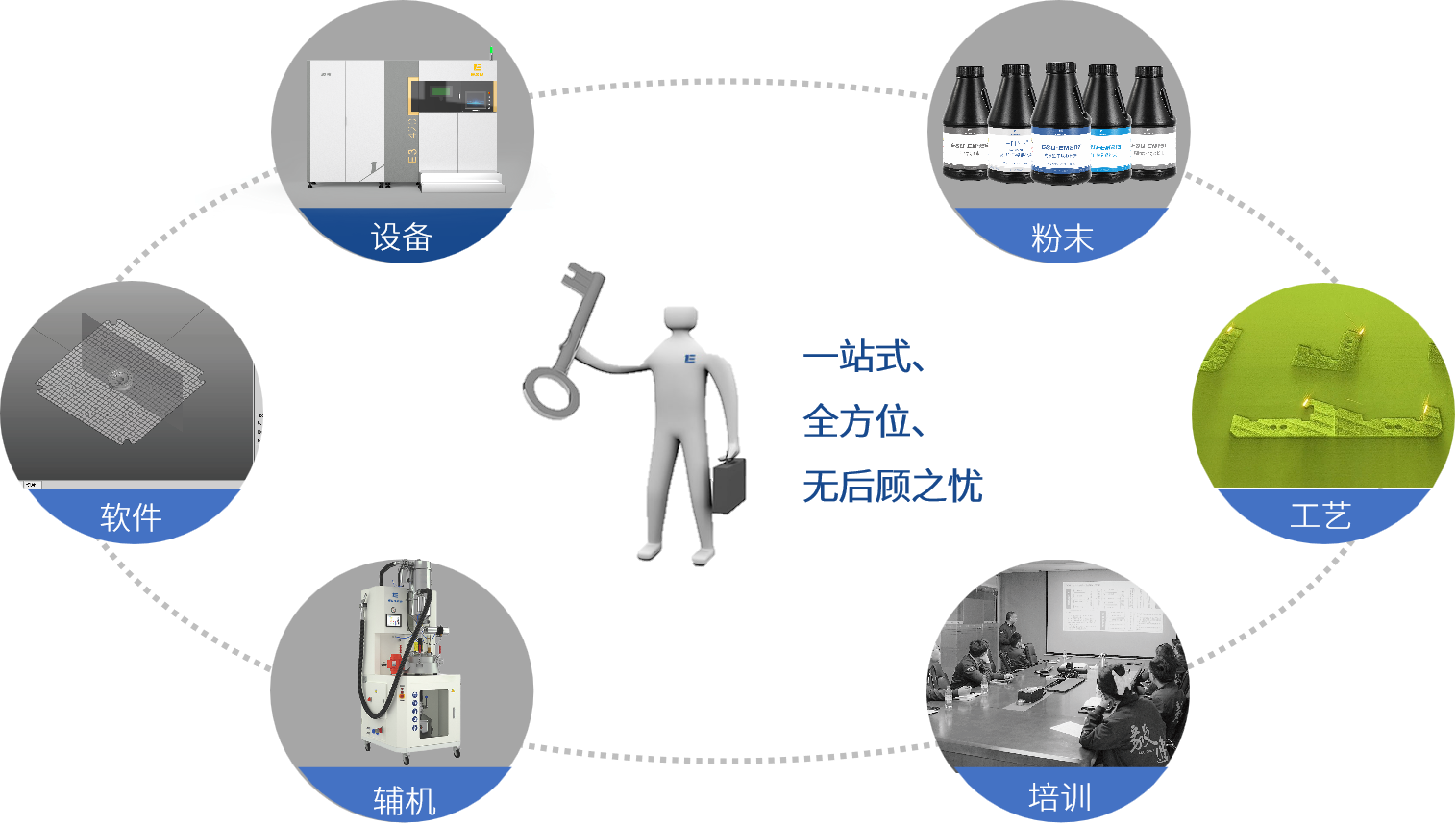
The Future of the Mold Industry: Accelerating the Transformation towards Additive Manufacturing
Today, the mold industry is experiencing a surging wave of transformation. The shoe mold industry has already introduced 3D printing equipment on a large scale, completely replacing traditional subtractive manufacturing. In the future, with the further improvement of printing efficiency and accuracy, 3D printing is bound to play an important role in more mold manufacturing fields. The future is already here, and there is no time to lose! Let's witness the wave of the 3D printing technology revolution together!